Creating a World Without Waste from East Kilbride
Credit: Coca-Cola Europacific Partners
Seamus Kerrigan, Operations Director at Coca-Cola Europacific Partners in East Kilbride, explains how the site is at the forefront of moving the business towards net zero by 2040.
Coca-Cola Europacific Partners’ (CCEP) manufacturing site in East Kilbride, Scotland has played a key role in many of the business’ major sustainability milestones and ‘firsts’ over the years.
From kicking off production for our bottles made from 100% recycled plastic when the business made the switch across our 500ml range last year, to leading on the transition from plastic to paper straws for our Capri-Sun pouches, East Kilbride has been right at the forefront of sustainable packaging innovation, every step of the way.
And now, East Kilbride will become the first site to manufacture our brand-new 1.5L bottles of Coca-Cola Zero Sugar, Diet Coke and Fanta with attached caps.
This innovative redesign means that the lid will remain attached to its bottle, wherever it goes, preventing it from being discarded or thrown away separately. This will make it easier than before to recycle the entire bottle, ensuring that as much plastic as possible is making its way back to recycle and ensure no caps get left behind.
Small steps
We are the first major soft drinks supplier to announce the switch to new attached caps to our plastic bottles across our entire portfolio. Starting here in East Kilbride, the full transition is set to be complete for all plastic bottles manufactured across our sites in GB by early 2024.
While it might sound like a small change, it’s one that will make a significant difference. The milestone forms part of our ongoing efforts to improve recycling rates, which is vital to increasing the amount of quality material being recovered that can be reused. Our ambition is to use 100% recycled plastic to make all of our bottles, so by ensuring they are being recycled we can start to increase our use of recycled material across all of our packaging. It is this ongoing innovation that will incrementally take us towards a circular economy and help us build a World Without Waste.
And these innovations are taking place right from here from East Kilbride – the site is a fantastic example of how, step by step, we can help to deliver a big impact. At our production site, we’ve been using 100% renewable energy for more than ten years, we’ve sent zero waste to landfill for the same period of time, and since 2010 we’ve reduced the site’s carbon footprint by 47%.
But these changes are all part of our larger ambition - CCEP’s This is Forward sustainability action plan, and feeds into the business’ overall social and environmental goals – including our 2040 net zero target.
As the producer of some of the most well-known and loved brands globally, we know it’s our responsibility to ensure we’re always innovating and moving forward by putting ourselves at the forefront of sustainable manufacturing innovation, no matter how small a change might seem.
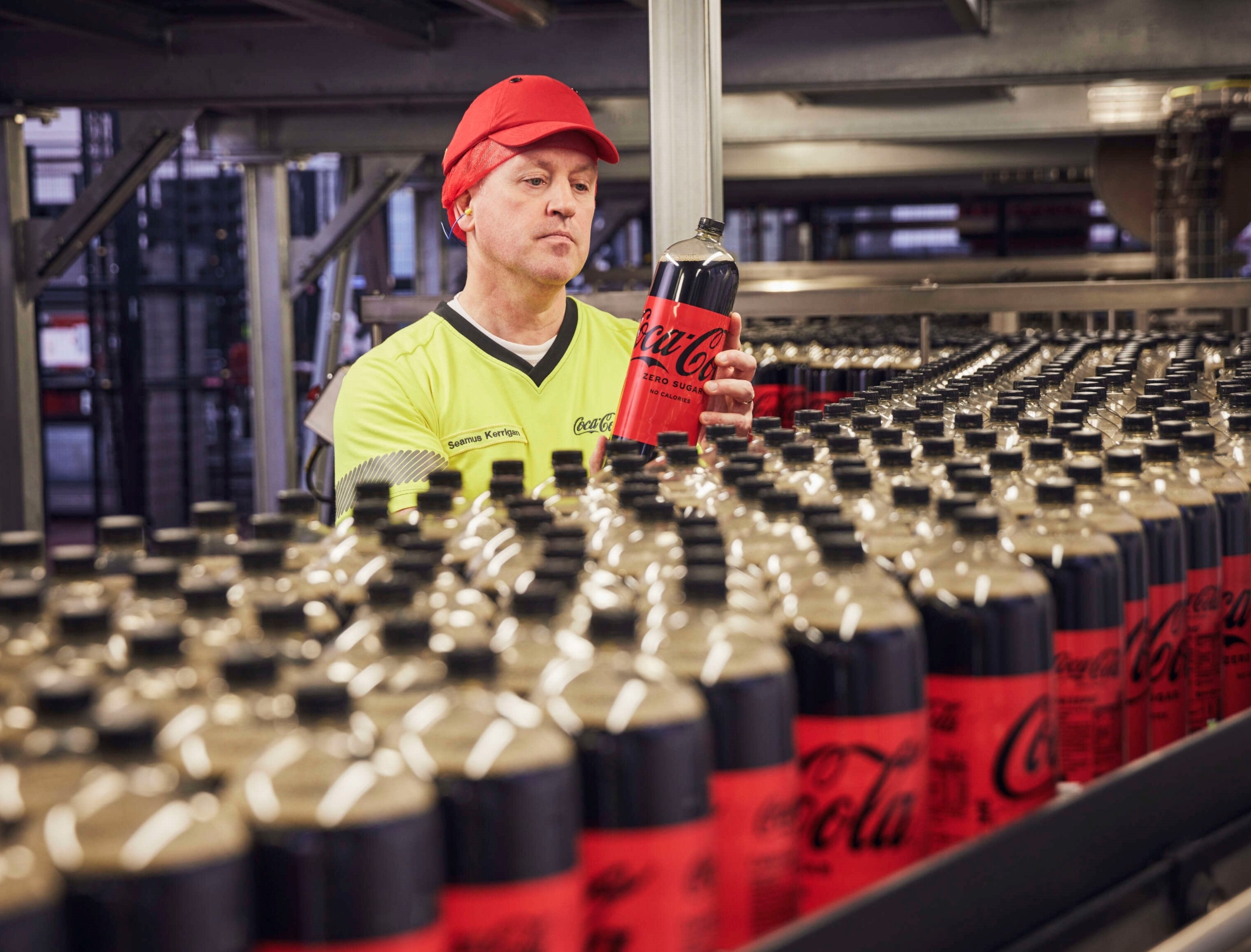
Working together
Working in manufacturing, I’ve always understood how important it is that all parts of the machine come together to run smoothly. This has certainly been true for our milestone switch to attached caps, which wouldn’t have been possible without the hard work and determination of all colleagues involved in making it happen. Our 200-strong workforce at the factory, as well as countless others across the business, have demonstrated what can be achieved through collaboration.
Elsewhere in the business, we’re working with industry partners on new innovations in sustainable packaging, such as paper bottles and refillables. Partners including CuRe Technology are helping us find new ways to provide a new lease of life for difficult to recycle polyester waste and we’ve previously recently invested in Lavit, a leading maker of multi-beverage, counter-top dispensing machines to explore and test new dispensed delivery solutions.
We’re also working with Circularity Scotland to support the implementation of an effective Deposit Return Scheme, which will help us to recover more high-quality plastic to be reused. These cross-industry partnerships are essential in accelerating our progress and journey to Net Zero.
Together with our colleagues, partners and customers, we’re shifting the dial on climate change and creating real change, one step at a time.