How our sustainability journey at Edmonton is helping to achieve net-zero
The progress at our Edmonton site demonstrates the power of small changes in reducing carbon emissions.
This week we’ve reached an exciting milestone at our site in Edmonton by becoming the first Coca-Cola Europacific Partners (CCEP) factory in Great Britain to manufacture 500ml plastic bottles with attached caps across our brands.
The roll out marks the next step in our sustainability journey, following the initial switch to attached caps on our larger, 1.5L bottles earlier this year. The new design means that the lid will remain attached to its bottle, wherever it goes, preventing it from being discarded or thrown away separately. It will make it easier than before to recycle the entire bottle, ensuring that as much plastic as possible is making its way back to recycle and that no caps get left behind.
You’ll see the change across bottles of Coca-Cola Zero Sugar, Diet Coke, and Fanta Zero, initially in stores and outlets in the south of the country, with plans to implement the change across our entire range sold in Great Britain by the end of 2024.
It might sound like just a small change, but as a format designed to be enjoyed while out and about, it’s even more important that the caps stay attached to our 500ml plastic bottles, instead of ending up anywhere they aren’t supposed to. Combined with the fact that our bottles are 100% recyclable, and made from 100% recycled plastic* this amounts to a huge quantity of plastic being prevented from becoming waste, and instead being recycled, helping us drive towards achieving a circular economy.
The move forms part of our sustainability ambition, CCEPs This is Forward sustainability action plan, and helps us move one step closer to our all important 2040 net zero target.
A little goes a long way
All of this is happening from right here in Edmonton – our only site within the M25. We started production of our first 500ml plastic bottles with attached caps this week. In time, we’ll see the change rolled out across our other factory sites in GB including Sidcup and Wakefield. It really does show the power that small changes can have.
I like to think that this is something we know a lot about at Edmonton – the power of small changes.
We recently achieved a milestone 70% reduction in carbon emissions compared with 2010 levels. This is the result of many incremental steps at the site to increase efficiency, reduce waste and improve processes. We’ve been using 100% renewable electricity for over 10 years, including via a solar panel array on our factory roof, and we’ve not sent any waste to landfill for just as long. We also recently replaced all material handling equipment (MHE), such as forklift trucks, with new models powered by lithium-ion batteries, which produce no carbon emissions in their day-to-day operations.
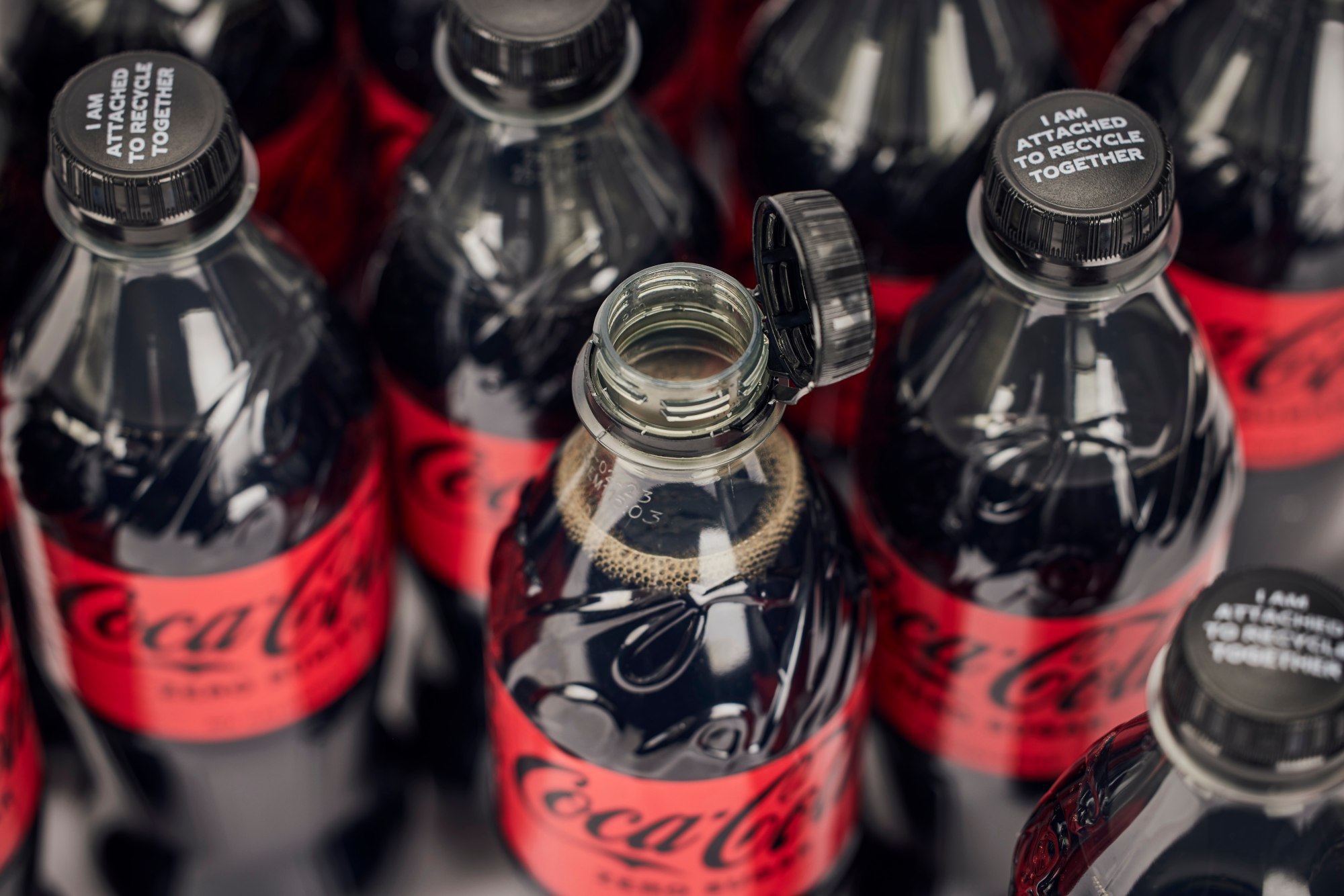
A recent £3m investment has allowed us to convert our existing lines to produce 500ml plastic bottles with attached caps. We’ve also invested £5.8m in a rear door loading facility, which has doubled the number of loading bays at the site, and increased overall capacity by 22%.
This takes our overall investment at the site to £42m since 2017, and we’ve come a long way since then. We’re currently on a journey to gaining a carbon neutral status, and it’s these investments and steps like these that are helping us to make that happen.
I’m proud of the changes that each and every one of the 280 employees has contributed to at Edmonton to reduce emissions so far. The work we’ve put in here will eventually help make a difference across Great Britain in improving recycling rates and, one day, help us to achieve a World Without Waste.
* Excluding labels and caps